4月21日,從中國海油天津分公司獲悉,隨著12英寸雙金屬復合海底管線終止封頭入水,渤海首個千億方大氣田——渤中19-6凝析氣田 I期開發項目海底管線平管段全部鋪設完畢,并創下鋪設我國最高壓力等級海底管線、渤海油氣田最長海底輸氣管線以及完成渤海灣首個海底管線定向鉆穿越工程等新紀錄,為項目按期投產奠定基礎。
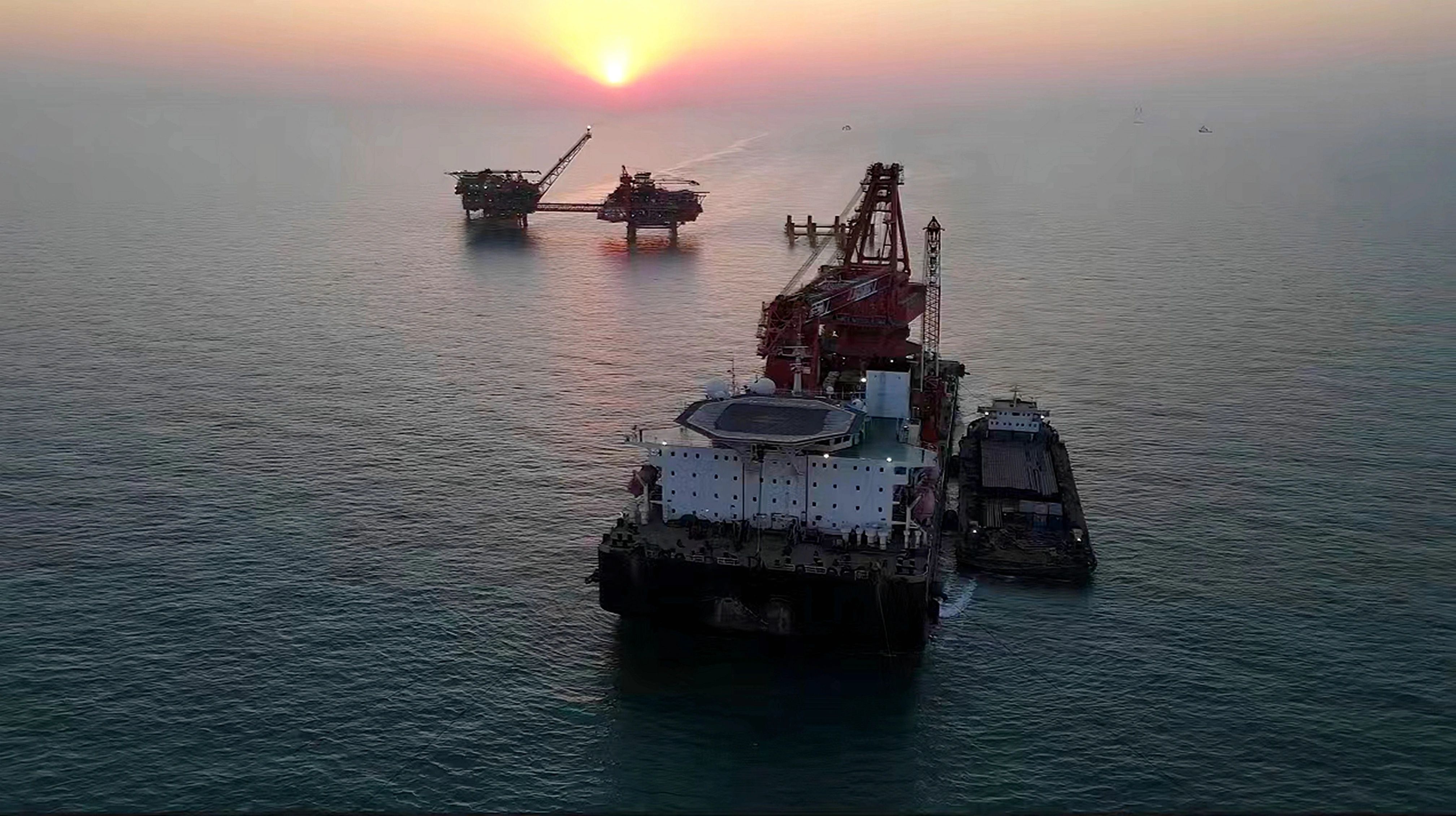
據了解,本次鋪設完工的海底管線將在山東省濱州市沿岸登陸,與陸地管線貫通后,連接到氣田“登陸”后的第一站濱州終端。該項目共有8條海底管線,總長約136公里。其中,7條海底管線穿梭于平臺間,總長約52公里,去年9月開始作業,歷時176天鋪設完成。1條起于平臺、止于山東濱州的天然氣長輸管線,是氣田海上油氣外輸的“大動脈”,長約84公里 ,采用兩條鋪管船由陸向海、由海向陸的雙向對鋪方案,為渤海油氣田目前最長海底對陸輸氣管線 ,今年1月開始施工,歷時104天鋪設完成。
這是迄今為止渤海油氣田施工難度最大、工藝最復雜的海底管線鋪設項目 。作業時間橫跨渤海冬季,風大浪疾,海況十分惡劣,待機時間高達50%;作業海域海底管線錯綜復雜,需要穿越重重管網,海管交叉跨越多達23次;所涉海管規格多,施工作業費時費力,其中3條為我國壓力等級最高海底管線,需要焊接13遍才能填充好一道焊縫,3條雙金屬不銹鋼復合管由于焊接工藝十分繁瑣,一天只能鋪設十幾根;海管登陸需要穿越向海延伸約0.5公里人工回填碎石區、海床以上7米高的防波堤,并避開規劃航道,在渤海灣首次實施復雜地質環境條件下定向鉆回拖海管登陸技術 ……
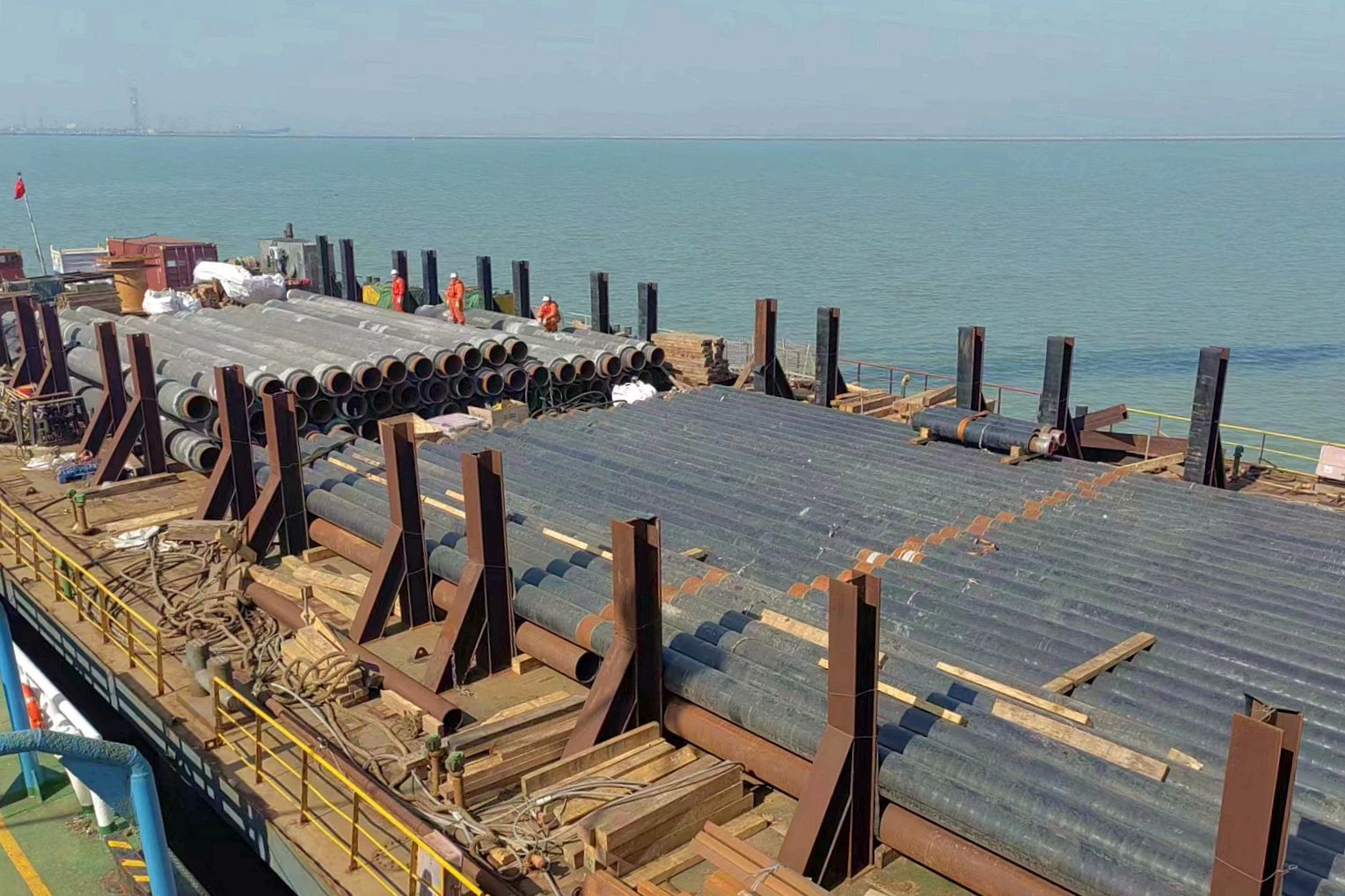
自去年9月開工以來,中國海油項目團隊有針對性地制定應對策略,健全跟蹤反饋機制,提高技術方案管理等級,強化安全、質量和進度管控,多措并舉全力保障項目按期實施。
據海油工程渤中19-6凝析氣田I期開發工程項目總經理鞠文杰 介紹,項目成立由技術專家牽頭的攻關團隊,攻克超高壓海底管線材料與選型設計、復雜工況臨界結構設計、大壁厚高壓管線高效焊接工藝開發等一系列難題,實現了從材料、設計、工藝到施工的全面自主化、國產化;采用全自動焊焊接工藝,協調安排自動焊設備,并利用項目轉場、天氣待機等施工間歇,見縫插針進行焊工技能培訓和考試取證,有效緩解自動焊工設備和人員不足狀況,大幅提高焊接效率;針對定向鉆施工經驗不足等問題,項目多次深入現場實地考察和反復溝通,逐一梳理演練施工細節,創新性開發出預鋪法加整體回拖相結合的定向鉆技術新工藝,大幅降低了渤海海域特殊地層應用定向鉆回拖海管的施工風險。
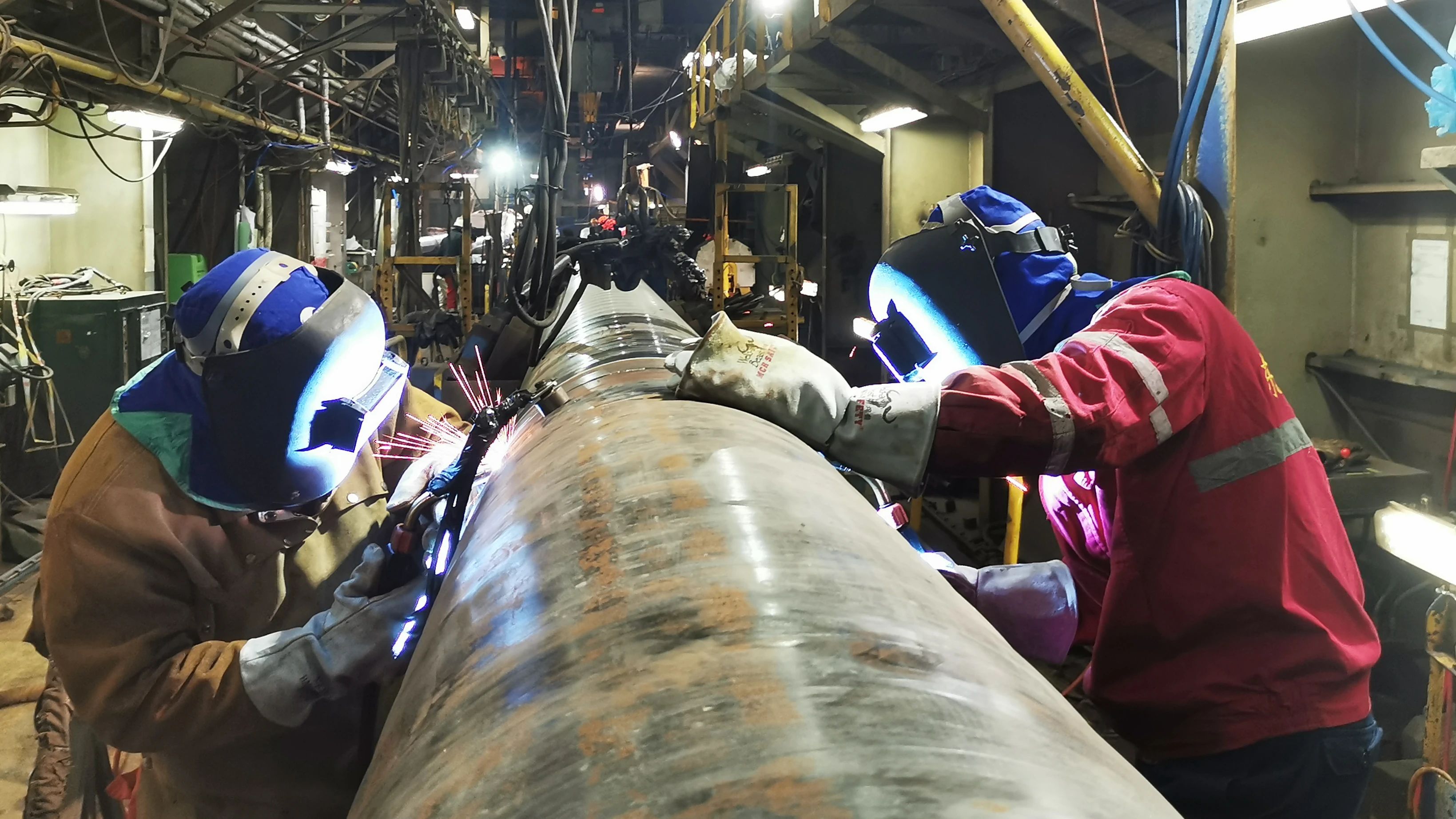
渤中19-6凝析氣田 位于渤海中部海域,是我國東部第一個大型、整裝、高產、特高含凝析油的千億方凝析氣田 ,目前已探明天然氣地質儲量超2000億立方米、探明凝析油地質儲量超2億立方米。
據中國海油天津分公司工程建設中心渤西區域項目組項目經理萬文濤 介紹,“I期開發項目是國家天然氣產供儲銷體系建設重點項目,也是渤海油氣田深入貫徹落實黨的二十大精神、加大油氣資源勘探開發和增儲上產力度的重要擴能工程,預計投產后日輸氣容量約760萬立方米,同時將生產丙烷、丁烷、LPG、穩定輕烴、干冰等產品,為京津冀及環渤海地區提供穩定可靠的綠色能源和化工產品。”